Continuous Distillation
Categories: Lab EquipmentContinuous Distillation Main characteristics of the pilot Industrial instrumentation Flow switch of the condenser cooling water for operators safety. Level and temperature switches to protect heat...
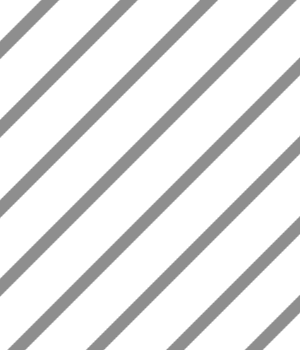
Product
Description
Continuous Distillation
Main characteristics of the pilot
- Industrial instrumentation
- Flow switch of the condenser cooling water for operators safety.
- Level and temperature switches to protect heating element.
- Borosilicate glass and stainless steel AISI 316L manufacturing
- Rigid process pipes
- Electrical heating Variable reflux column head controlled by ATEX solenoid valve.
Principal of Working:
Distillation allows the separation of a mixture of compounds each having different boiling points. Boiling the mixture makes it possible to collect the vapours of the different components of the liquid. Multiple re-condensation and re-evaporation progressively enriches the vapour phase with the most volatile product. The column packing greatly increases the exchange area and thus the mass transfer. A metering pump used to introduce the solution at precise points in the column (⅓ and ⅔ of the way up) allows this unit operation to take place continuously. The vapours are condensed and then divided between distillate and reflux via the column head and its globe valve. The residue is collected in a continuous way at the bottom of the boiler. The temperatures at the bottom and the head of the column are measured, and also at the points where the solution is introduced, so as to determine the temperature profile.
Teaching objectives
- Study of the following experimental parameters:
- Study of column hydrodynamics.
- Influence of operating conditions on separation of a binary solution.
- Calculations:
- Heat balances.
- Mass balance.
- Determination of number of theoretical plates (McCABE and THIELE, PONCHON and SAVARIT).
- Determination of number of transfer units
Technical specifications
Equipment:- Polyethylene feed solution tank.
- Feed solution metering pump, AISI 316L stainless steel body, P.T.F.E. diaphragm, manual control.
- Feed pre-heater with two valves for feed at 33% or 66% of the column, fitted with a low level safety switch and a high temperature safety switch.Borosilicate glass continuous boiler, electric heating, fitted with low level safety switch and high temperature safety switch.
- Coolant for differential pressure measurement.
- Borosilicate glass column in three pieces with “MULTIKNIT” type packing in AISI 316L stainless steel.
- Three AISI 316L stainless steel plates, each fitted with a sampling valve and a temperature plug.
- Borosilicate glass column head, with temperature plug, fitted with a solenoid timer valve to control the reflux rate.
- Vertical condenser, borosilicate glass body, AISI 316L stainless steel exchanger, single effect with baffles.
- Two AISI 316L stainless steel distillate and residue coolers.
- Borosilicate glass residue receiver tank, fitted with a drain valve in AISI 316L stainless steel.
- Borosilicate glass distillate receiver tank, fitted with a drain valve in AISI 316L stainless steel.
- Two polyethylene distillate and residue collection tanks.
- AISI 316L stainless steel connecting tubes for the process and reinforced PVC tube for cooling fluid.
- Support framework with AISI 304L stainless steel tubes, aluminium connecting nuts and adjustable feet.
Instrumentation:
- Cooling water feed to condenser fitted with variable area flowmeter with its adjusting valve and water flow switch to turn off heating in case of lack of cooling water.
- Measurement of the column pressure drop by differential “U” type manometer.
- IP55 command and control cabinet fitted with emergency stop, operating buttons and the following interfaces:
- Preheating temperature controller.
- Electronic timer controlling valve at the head of the column.
- Boiler heating controller.
- Two digital temperature indicators with eleven Pt100 Ω type probes.
Dimensions and weight
- 1400 mm x 650 mm x 3050 mm ~ 180 kg.
Essential requirements
- 230 V / 50 Hz / Single phase:4 kW.
- Cold water 20°C / 3 bar: 1 m3/h.
- Drain.
quick overview :
Continuous Distillation
Main characteristics of the pilot
- Industrial instrumentation
- Flow switch of the condenser cooling water for operators safety.
- Level and temperature switches to protect heating element.
- Borosilicate glass and stainless steel AISI 316L manufacturing
- Rigid process pipes
- Electrical heating Variable reflux column head controlled by ATEX solenoid valve.
Principal of Working:
Distillation allows the separation of a mixture of compounds each having different boiling points. Boiling the mixture makes it possible to collect the vapours of the different components of the liquid. Multiple re-condensation and re-evaporation progressively enriches the vapour phase with the most volatile product. The column packing greatly increases the exchange area and thus the mass transfer. A metering pump used to introduce the solution at precise points in the column (⅓ and ⅔ of the way up) allows this unit operation to take place continuously. The vapours are condensed and then divided between distillate and reflux via the column head and its globe valve. The residue is collected in a continuous way at the bottom of the boiler. The temperatures at the bottom and the head of the column are measured, and also at the points where the solution is introduced, so as to determine the temperature profile.
Teaching objectives
- Study of the following experimental parameters:
- Study of column hydrodynamics.
- Influence of operating conditions on separation of a binary solution.
- Calculations:
- Heat balances.
- Mass balance.
- Determination of number of theoretical plates (McCABE and THIELE, PONCHON and SAVARIT).
- Determination of number of transfer units
Technical specifications
Equipment:- Polyethylene feed solution tank.
- Feed solution metering pump, AISI 316L stainless steel body, P.T.F.E. diaphragm, manual control.
- Feed pre-heater with two valves for feed at 33% or 66% of the column, fitted with a low level safety switch and a high temperature safety switch.Borosilicate glass continuous boiler, electric heating, fitted with low level safety switch and high temperature safety switch.
- Coolant for differential pressure measurement.
- Borosilicate glass column in three pieces with “MULTIKNIT” type packing in AISI 316L stainless steel.
- Three AISI 316L stainless steel plates, each fitted with a sampling valve and a temperature plug.
- Borosilicate glass column head, with temperature plug, fitted with a solenoid timer valve to control the reflux rate.
- Vertical condenser, borosilicate glass body, AISI 316L stainless steel exchanger, single effect with baffles.
- Two AISI 316L stainless steel distillate and residue coolers.
- Borosilicate glass residue receiver tank, fitted with a drain valve in AISI 316L stainless steel.
- Borosilicate glass distillate receiver tank, fitted with a drain valve in AISI 316L stainless steel.
- Two polyethylene distillate and residue collection tanks.
- AISI 316L stainless steel connecting tubes for the process and reinforced PVC tube for cooling fluid.
- Support framework with AISI 304L stainless steel tubes, aluminium connecting nuts and adjustable feet.
Instrumentation:
- Cooling water feed to condenser fitted with variable area flowmeter with its adjusting valve and water flow switch to turn off heating in case of lack of cooling water.
- Measurement of the column pressure drop by differential “U” type manometer.
- IP55 command and control cabinet fitted with emergency stop, operating buttons and the following interfaces:
- Preheating temperature controller.
- Electronic timer controlling valve at the head of the column.
- Boiler heating controller.
- Two digital temperature indicators with eleven Pt100 Ω type probes.
Dimensions and weight
- 1400 mm x 650 mm x 3050 mm ~ 180 kg.
Essential requirements
- 230 V / 50 Hz / Single phase:4 kW.
- Cold water 20°C / 3 bar: 1 m3/h.
- Drain.
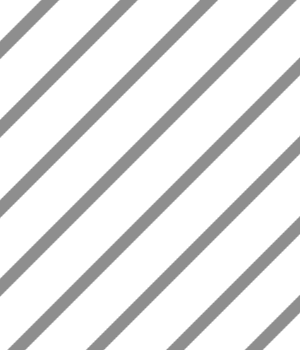
Product
Reviews
add Review
reviews
No Review Yet.
Product
Reviews
add Review
reviews
No Review Yet.