Multi-Function Process Control Teaching Style Electronic
Categories: Industrial Process LaboratoryDescription Basic Process Control System It contains everything that is needed to perform a range of single-loop process control experiments in conjunction with a PC. It includes a variable volume...
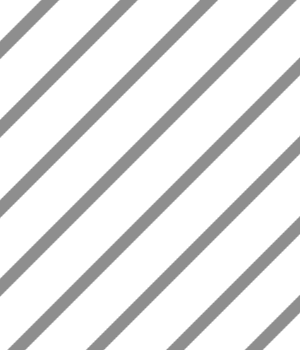
Product
Description
Description Basic Process Control System It contains everything that is needed to perform a range of single-loop process control experiments in conjunction with a PC. It includes a variable volume process tank, a hot water tank with electric heater and indirect heating/cooling coil, a hot water pump, two non-dedicated pumps, three on/off solenoid valves and a proportioning valve. The instrumentation includes temperature sensors, two differential water pressure sensors, a mechanical level sensor (float switch) and an electronic level sensor (conductivity). The inlets and outlets of the various pumps, valves and tanks incorporate self-sealing quick-release fittings. This enables the configuration to be quickly changed, offering a wide variety of different loops. It includes a computer interface (USB), and all of the parameters can be controlled directly from the computer, (i.e. the pump speeds), the valve positions and the heater power. The computer also displays the readings from the various measurement sensors. The software supplied with the unit includes on/off, time proportioned and proportional/integral/derivative (PID) algorithms where all the parameters are easily accessed and adjusted by the user. This approach means that a separate electronic console is unnecessary for most applications. The flexible nature of the system also enables a wide variety of different disturbances to be applied to the loops to permit the effectiveness of the control parameters to be compared. As all these disturbances are under software control, they can be repeated precisely during the optimization process, thus enabling an excellent degree of fine-tuning to be implemented. A pressure regulating valve with filter is also included to isolate the equipment from fluctuations in the water supply pressure. The Type Of Loops Achievable With The Basic Include: Tank water level by varying input flow Water flow rate by varying pump speed Temperature of water in a vessel by varying the heater power Temperature of water heated indirectly by varying the flow rate (All these loops are under software control) Process Vessel Accessory It extends the capability of the basic by adding an additional process vessel, complete with a heating/cooling coil and a stirrer. The inputs and outputs incorporate quick release fittings, enabling the added quickly and easily. This is also includes a conductivity probe to enable cost-effective fluid property demonstrations to be performed. The addition of the process vessel enables more complex process control problems to be addressed, including remote setpoint demonstrations. Again these all take place with the repeatability advantages that electronic and software control brings. Additional loops that can be implemented with it include: Single Loops in Combination:
- Conductivity control of reactor contents by varying flow rate of one component
- Temperature control of reactor contents by varying heating fluid flow rate
- Temperature control of heating fluid by varying heater power
- Ratio control of two flows
- Cascade control of conductivity and flow
- Feedforward control of flow to flow
- Feedforward control of flow combined with feedback control of conductivity (All these loops are under software control)
- Use of a commercial PID controller
- Simple interfacing to other PLC and/or PID controllers
- Use of four 20mA interfaces
- Use of serial communications (RS232) in a control system
- Simple SCADA demonstration (requires PC)
- A multi-function process control teaching system, capable of demonstrating level, flow, pressure and temperature control loops
- Bench mounted and includes a built-in USB computer interface
- Options include: reactor vessel with conductivity measurement, pH measurement, pneumatic control valve and electronic console
- Includes the following process control demonstrations:
- Calibration of sensors (via PC software)
- Inflow control
- Outflow control
- Direct heating
- Indirect heating
- Batch operation
- Continuous operation
- Effect of sensor lag (eg thermometer pocket)
- Effect of system time constant (eg volume change)
- Effect of dead time (eg holding tube)
- Effect of mixing/stirring
- Level – on/off switch (fixed hysteresis)
- Level – differential on/off switch (adjustable hysteresis)
- Level – proportional pressure sensor (slow system response)
- Flow – proportional turbine sensor
- Temperature – on/off switch (fixed hysteresis)
- Temperature – proportional thermocouple sensors
- Static pressure – proportional sensor (fast system response)
- Differential pressure – proportional pressure (fast system response)
- pH – proportional sensor
- On/off flow control via solenoid valves
- Time-proportioned flow control via solenoid valves
- Proportional flow control via pump speed
- Proportional flow control via electrical proportioning valve
- Proportional flow control via pneumatic proportioning valve
- On/off heater power control via solid state relay
- Time proportioned heater power control via solid state relay
- Proportional heater power control via solid state relay
- Manual control
- Effect of reverse/direct action
- On/off output with hysteresis
- Time proportioned output with adjustable P, I & D terms and cycle time
- PID proportional output with adjustable P, I & D terms
- Remote setpoint control
- Ratio, cascade and feedforward with feedback loops
quick overview :
Description Basic Process Control System It contains everything that is needed to perform a range of single-loop process control experiments in conjunction with a PC. It includes a variable volume process tank, a hot water tank with electric heater and indirect heating/cooling coil, a hot water pump, two non-dedicated pumps, three on/off solenoid valves and a proportioning valve. The instrumentation includes temperature sensors, two differential water pressure sensors, a mechanical level sensor (float switch) and an electronic level sensor (conductivity). The inlets and outlets of the various pumps, valves and tanks incorporate self-sealing quick-release fittings. This enables the configuration to be quickly changed, offering a wide variety of different loops. It includes a computer interface (USB), and all of the parameters can be controlled directly from the computer, (i.e. the pump speeds), the valve positions and the heater power. The computer also displays the readings from the various measurement sensors. The software supplied with the unit includes on/off, time proportioned and proportional/integral/derivative (PID) algorithms where all the parameters are easily accessed and adjusted by the user. This approach means that a separate electronic console is unnecessary for most applications. The flexible nature of the system also enables a wide variety of different disturbances to be applied to the loops to permit the effectiveness of the control parameters to be compared. As all these disturbances are under software control, they can be repeated precisely during the optimization process, thus enabling an excellent degree of fine-tuning to be implemented. A pressure regulating valve with filter is also included to isolate the equipment from fluctuations in the water supply pressure. The Type Of Loops Achievable With The Basic Include: Tank water level by varying input flow Water flow rate by varying pump speed Temperature of water in a vessel by varying the heater power Temperature of water heated indirectly by varying the flow rate (All these loops are under software control) Process Vessel Accessory It extends the capability of the basic by adding an additional process vessel, complete with a heating/cooling coil and a stirrer. The inputs and outputs incorporate quick release fittings, enabling the added quickly and easily. This is also includes a conductivity probe to enable cost-effective fluid property demonstrations to be performed. The addition of the process vessel enables more complex process control problems to be addressed, including remote setpoint demonstrations. Again these all take place with the repeatability advantages that electronic and software control brings. Additional loops that can be implemented with it include: Single Loops in Combination:
- Conductivity control of reactor contents by varying flow rate of one component
- Temperature control of reactor contents by varying heating fluid flow rate
- Temperature control of heating fluid by varying heater power
- Ratio control of two flows
- Cascade control of conductivity and flow
- Feedforward control of flow to flow
- Feedforward control of flow combined with feedback control of conductivity (All these loops are under software control)
- Use of a commercial PID controller
- Simple interfacing to other PLC and/or PID controllers
- Use of four 20mA interfaces
- Use of serial communications (RS232) in a control system
- Simple SCADA demonstration (requires PC)
- A multi-function process control teaching system, capable of demonstrating level, flow, pressure and temperature control loops
- Bench mounted and includes a built-in USB computer interface
- Options include: reactor vessel with conductivity measurement, pH measurement, pneumatic control valve and electronic console
- Includes the following process control demonstrations:
- Calibration of sensors (via PC software)
- Inflow control
- Outflow control
- Direct heating
- Indirect heating
- Batch operation
- Continuous operation
- Effect of sensor lag (eg thermometer pocket)
- Effect of system time constant (eg volume change)
- Effect of dead time (eg holding tube)
- Effect of mixing/stirring
- Level – on/off switch (fixed hysteresis)
- Level – differential on/off switch (adjustable hysteresis)
- Level – proportional pressure sensor (slow system response)
- Flow – proportional turbine sensor
- Temperature – on/off switch (fixed hysteresis)
- Temperature – proportional thermocouple sensors
- Static pressure – proportional sensor (fast system response)
- Differential pressure – proportional pressure (fast system response)
- pH – proportional sensor
- On/off flow control via solenoid valves
- Time-proportioned flow control via solenoid valves
- Proportional flow control via pump speed
- Proportional flow control via electrical proportioning valve
- Proportional flow control via pneumatic proportioning valve
- On/off heater power control via solid state relay
- Time proportioned heater power control via solid state relay
- Proportional heater power control via solid state relay
- Manual control
- Effect of reverse/direct action
- On/off output with hysteresis
- Time proportioned output with adjustable P, I & D terms and cycle time
- PID proportional output with adjustable P, I & D terms
- Remote setpoint control
- Ratio, cascade and feedforward with feedback loops
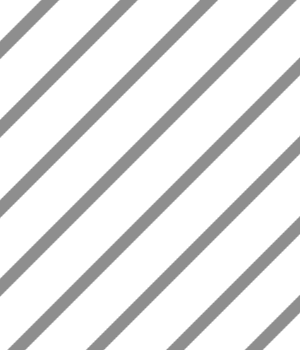
Product
Reviews
add Review
reviews
No Review Yet.
Product
Reviews
add Review
reviews
No Review Yet.